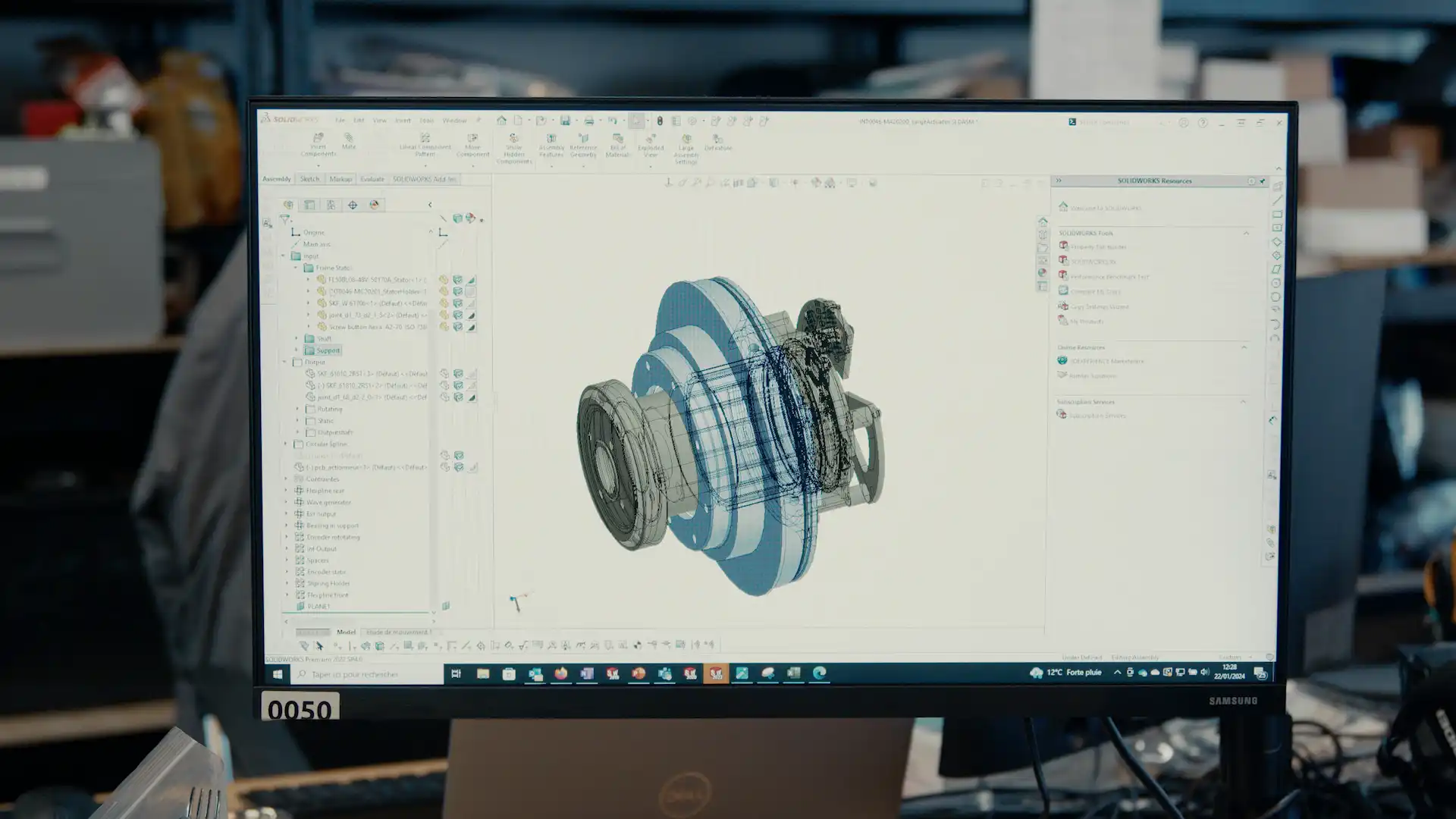
Clear information on the industrialization of high-tech products can be elusive, whether you’re an investor, an advisor to company, or just curious about embarking on a hardware project or its initial ideation. This introductory article aims to provide a straightforward and concise overview without delving into excessive detail

Industrialization is a rigorous process designed to transform a functional prototype into a product ready for manufacturing. The term “industrialize” refers to the application of industrial methods for production or operation.
There are various approaches to this process, but we will focus on one particular method we endorse. This method involves multiple iterative and successive phases, known as EVT (Engineering Verification Test), DVT (Design Verification Test), and PVT (Production Verification Test), which represent different levels of system maturity and stages of the manufacturing process. Industrialization kicks off after the Proof Of Concept (POC) and may continue even post-delivery through continuous improvement initiatives.
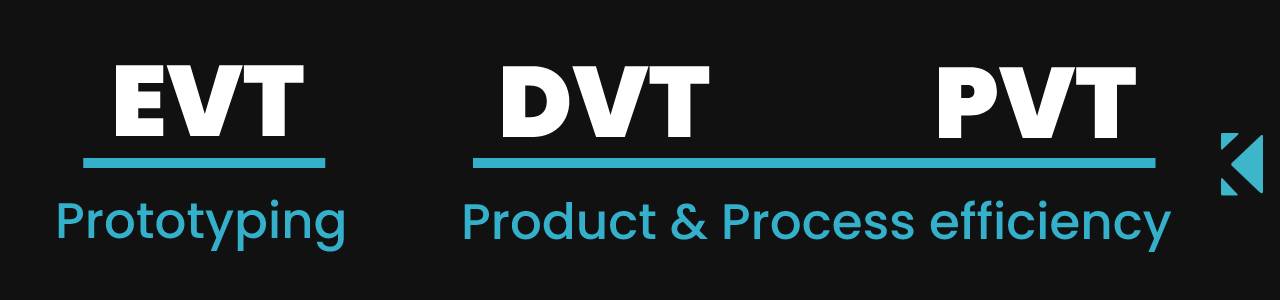
EVT
EVT : Engineering Verification / Validation & testing
->This is the validation stage for technical solutions.
EVT serves as the critical validation stage for technical solutions within the product development process.
During EVT, a single demonstrator is created that encompasses both “looks like” and “works like” prototypes, utilizing temporary components such as duplicate silicone parts, 3D-printed soft tooling, and PCBA prototypes. This stage is essential for verifying that the prototype operates with all functionalities outlined in the product requirements document (PRD) and that the design fulfills the intended purpose of the product. It’s crucial at this point to confirm that the product’s function is correctly defined.
The number of EVT prototypes produced varies based on the product’s complexity and the cost of the bill of materials (BOM), typically ranging from 3 to 10 units.
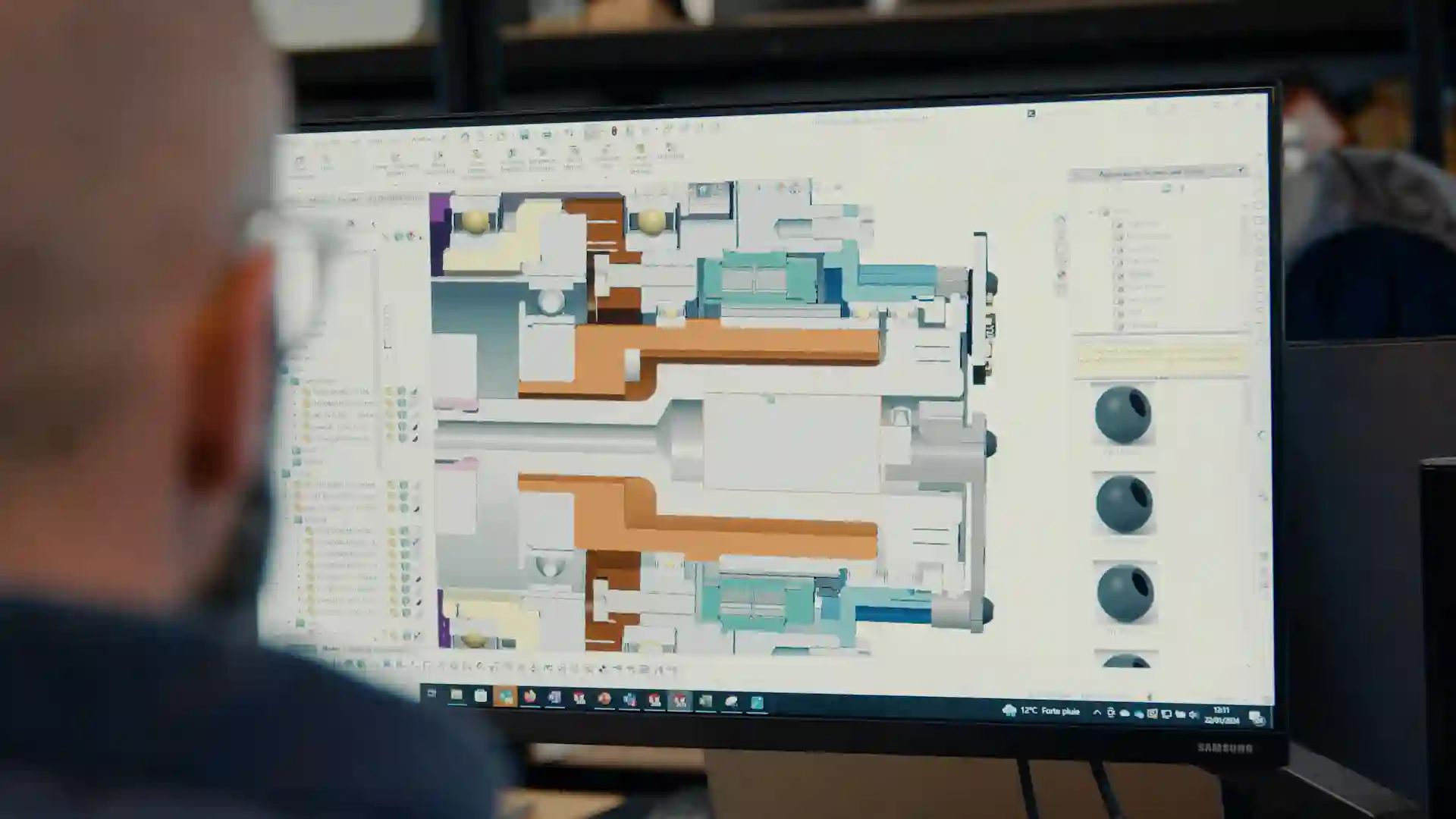
DVT
DVT : Design Verification / validation & testing
->The product validation stage
The DVT phase kicks off once we confirm that the design is feasible. At this point, all 3D and 2D drawings are finalized, materials are selected, and a comprehensive test plan is established. The DVT products represent the final production design configuration, incorporating components made using the actual production tools and molds. These designs are tested using real parts that are true to size and made from materials that closely resemble the final ones.
In this phase, the product is produced in limited quantities and subjected to extensive testing—including drop tests, heat resistance, and wear tests—to ensure it meets both aesthetic standards and environmental durability requirements.
This stage is crucial for obtaining necessary certifications and solidifying relationships with suppliers.
In essence, we assemble, test, and refine the design repeatedly until it meets all specifications. By the end of the DVT phase, all tests are formally documented, and the design specifications are finalized.
Quantities: The number of units produced varies depending on the product’s complexity and the cost of the bill of materials (BOM), typically ranging from 50 to 100.
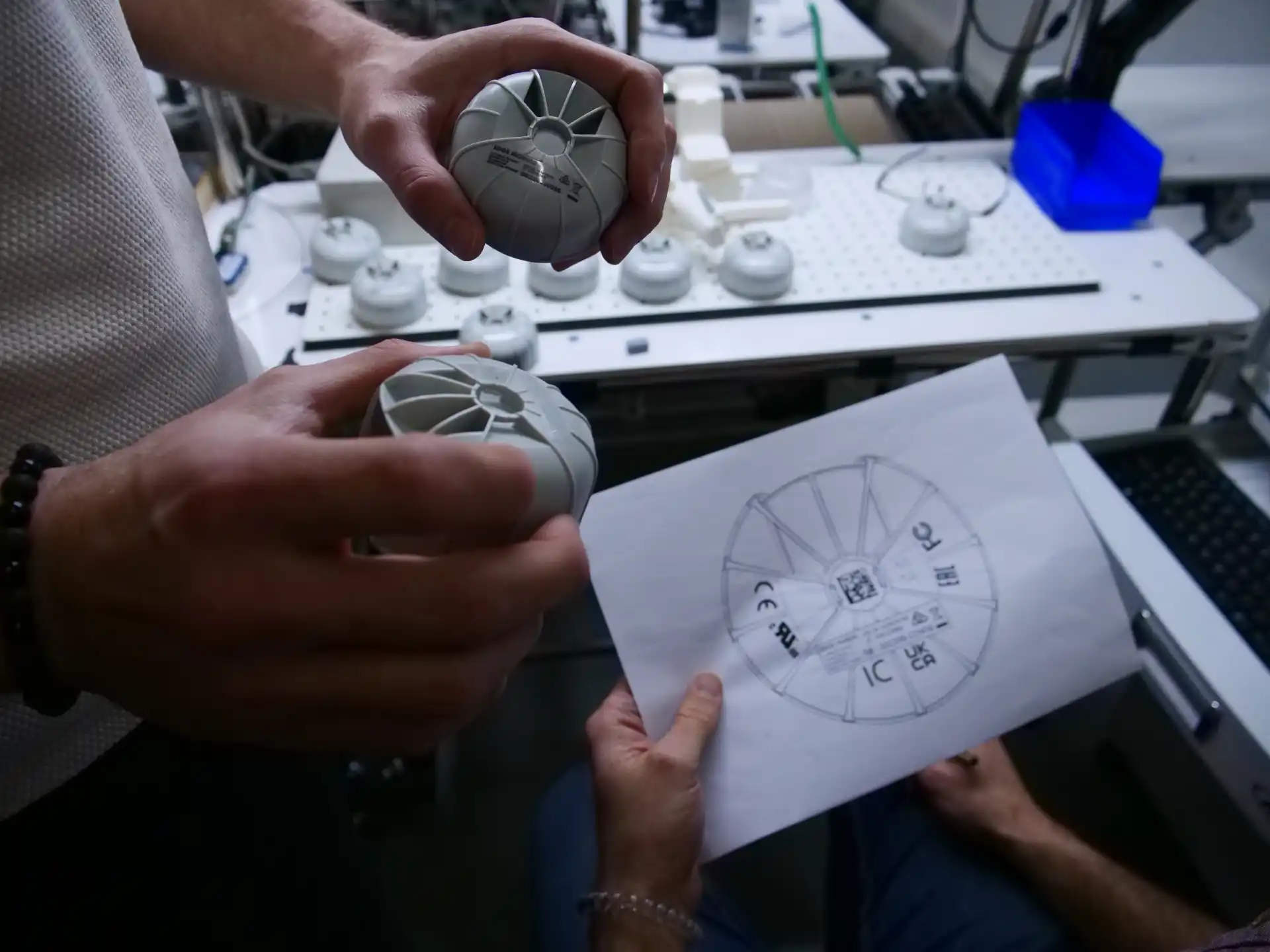
PVT
PVT : Product – Production Verification / Validation & Testing
->This is the production line validation stage (pre-series -> first run):
The PVT stage marks the final steps in product construction, where the manufactured units are anticipated to be sold to customers, pending successful testing. While these parts closely resemble those used in series production, they are still assembled by hand. Generally, PVT acts as a bridge to the ramp-up and mass production phase. A pilot production line is established to ensure that there are no failures across any stage of the production chain.
During PVT, the assembly process is thoroughly validated, examining factors such as process speed, quality, control points, test equipment, calibration tools, production monitoring, worker skills training, packaging, and the management of supply and logistics flows. Continuous improvement strategies such as PDCA (Plan-Do-Check-Act) and AMDEC (Failure Mode, Effects, and Criticality Analysis) in manufacturing are implemented to facilitate future developments and optimizations. This phase is more operationally focused than developmentally.
Quantities: The production volume during this phase depends on the product’s complexity and the cost of the bill of materials (BOM), generally ranging from 100 to 1000 units.
What’s next? Transition to series production.

To conclude
Navigating the journey from concept to consumer-ready product involves a meticulous process of validation and testing at each stage of product development. Starting with EVT, where the focus is on verifying the technical and functional feasibility of a prototype, through DVT, where the product design is refined and rigorously tested against real-world standards, and culminating in PVT, where production systems are validated and the product is prepared for mass manufacturing. Each phase—EVT, DVT, and PVT—plays a crucial role in ensuring that the final product not only meets the design specifications but also adheres to quality, safety, and regulatory standards before hitting the market.
By understanding and implementing these critical verification and validation stages, manufacturers can enhance product reliability, streamline production processes, and ultimately provide higher quality products to their customers. This structured approach to product development ensures that each component is tested and validated, thereby minimizing risks and maximizing product success in competitive markets.
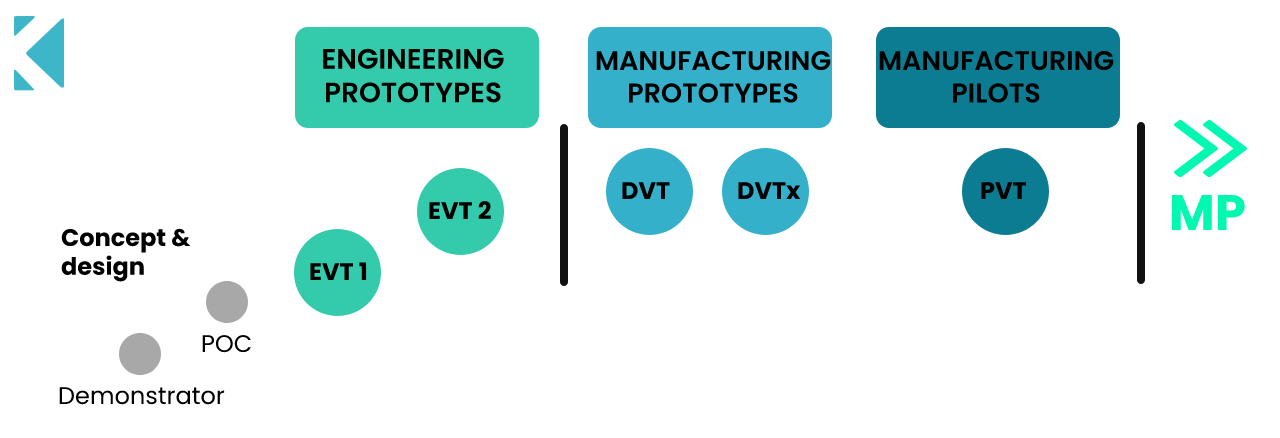
Recent Comments