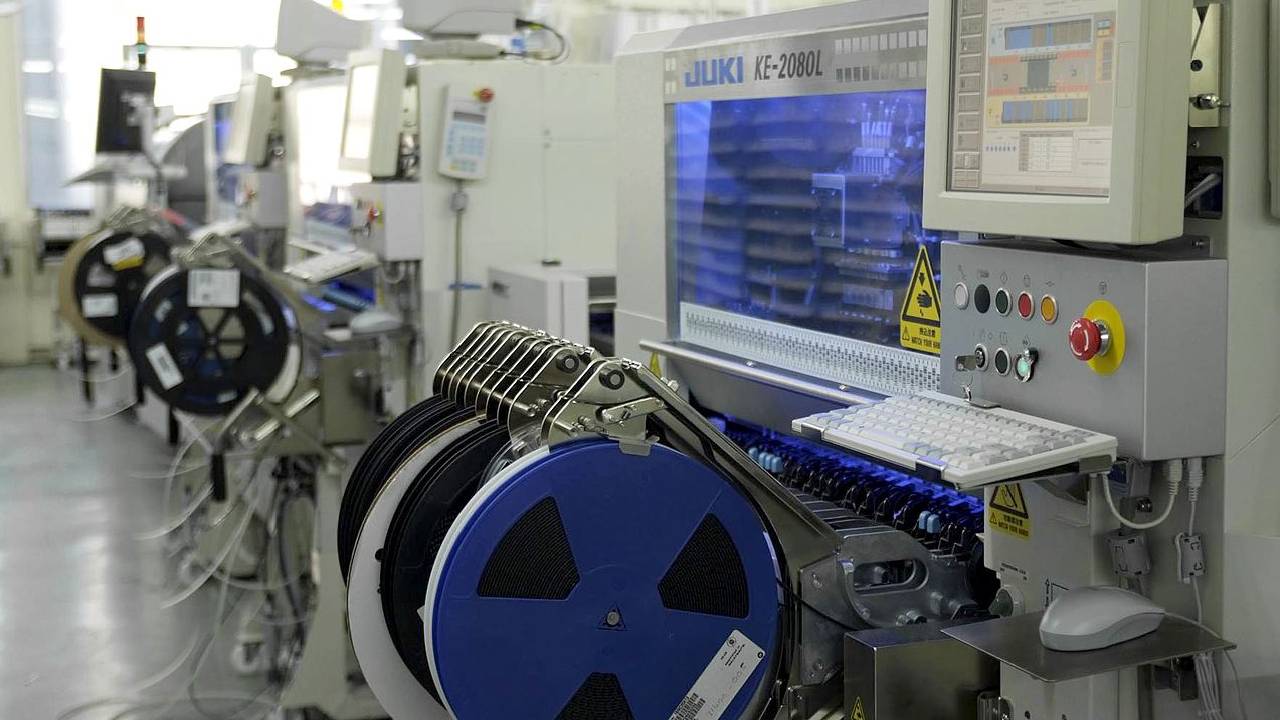
Ligne SMT
Dossier réalisé avec l’aide précieuse et attentionnée de Thibault Lestavel, ingénieur chez Kickmaker.
Dans ce dossier, vous découvrirez ce qui compose une ligne d’assemblage SMT (= Surface Mount Technology) qui est une méthode de production de circuits imprimés – et par extension un process applicable à l’assemblage d’un produit principalement électronique. Vous y découvrirez les différentes étapes qui composent cette méthode et les technologies employées. Cet exemple se veut généraliste qui ne saurait être considéré comme l’unique façon de faire.
Bonne lecture !
Sommaire
Contrôle d’entrée et stockage
Ligne d’assemblage PCB et SMT
Assemblage et tests fonctionnels
Expédition du matériel, IQC et stockage
Le matériel peut être expédié par plusieurs fournisseurs, directement à l’EMS. Cela inclut notamment :
- les composants électroniques (résistances, condensateurs, circuits intégrés, connecteurs…) ;
- les composants mécaniques (pièces plastique, vis…) ;
- les autres types de composants (batteries, moteurs, colle …).
Le packaging de ces composants doit rester fonctionnel tant pour garantir la qualité du stockage que pour conserver une bonne productivité. Bien que les coûts de stockage soient calculés sur le volume brut de l’emballage, il faut garder à l’esprit l’arbitrage à faire entre optimisation du packaging sur la ligne de production (bobinage, carton unitaire…) et celui nécessaire au stockage (ex : gros cartons de stocks).
Cela doit être pris en compte au début du projet en considérant la façon dont le produit va être assemblé, pour ne pas avoir à changer le type d’emballage dans l’usine.
IQC (incoming quality control) : contrôle de qualité d’entrée des composants
Ces composants sont soumis à un contrôle de qualité d’entrée (IQC) afin de s’assurer qu’ils correspondent à la fois aux critères des clients et des EMS en terme d’esthétique, d’emballage, etc…
L’IQC peut également inclure des tests fonctionnels basiques ainsi que des contrôles par échantillonnages sélectifs, toujours pour s’assurer que le composant correspond aux tolérances de conception.
Bien que l’échantillonnage fasse souvent partie des bonnes pratiques des EMS, il est également important de définir des critères de contrôle qualité en fonction de la criticité de la conception ainsi que du niveau de confiance envers les fournisseurs.
Par exemple, si une variabilité dans les lots de prototypes d’un fournisseur nouvellement qualifié est remarquée, cela peut être intéressant d’ajouter un contrôle spécial pour les premiers mois de production, afin de s’assurer que le les problèmes de variabilité sont désormais sous contrôle. Ces étapes de contrôle doivent être spécifiées pour une durée et un taux d’échantillonnage. Une surqualification, c’est-à-dire un trop grand nombre de critères d’inspection par rapport à un grand nombre d’échantillons entraîne directement un surcoût inévitable.
Stockage
Avant d’être stockées, les marchandises entrantes sont le ré-étiquetées et scannées pour correspondre à l’ERP de l’usine et assurer une traçabilité adéquate.
Le stockage doit être fait dans de bonnes conditions, prenant en compte les spécifications des différents composants. Par exemple, les composants électroniques nécessitent souvent un contrôle de température et d’humidité. Cela est d’autant plus applicable aux composés chimiques tels que la colle, la pâte à braser etc. En plus des contrôles de température et d’humidité, ces composants nécessitent également un environnement chimiquement contrôlé et ont une date limite d’utilisation.
Ligne d’assemblage PCB et SMT
Paste dispenser
Le circuit imprimé étant considéré ici comme un élément manufacturé extérieur, il est soumis au process de la section précédente.
Le parcours du circuit imprimé commence par le dépôt de la pâte à braser qui est un produit chimique à base d’étain, qui fond dans le four à refusion afin de créer les soudures. Le choix de la pâte à braser est critique et doit correspondre aux profils thermiques du four à refusion. Une mauvaise sélection de la pâte à braser peut entraîner des soudures de mauvaise qualité comme des soudures sèches ou l’apparition de bulles d’air.
Ces problèmes d’assemblage ne sont la plupart du temps pas détectables par les testeurs optiques ou fonctionnels, mais peuvent être repérés sous rayons X ou par d’autres procédés destructeurs de contrôle qualité. Par conséquent, il est important d’effectuer des contrôles qualité par échantillonnage, au début du processus pour s’assurer que ce dernier est sous contrôle, mais également durant la production.
Une fois que la pâte à braser est déposée, le convoyeur s’arrête à la machine “pick and place”. Un bras robotique saisit les composants électroniques à partir de différentes bobines et les dépose sur les empreintes du circuit imprimé. Cette machine peut déposer jusqu’à 50 000 composants par heure !
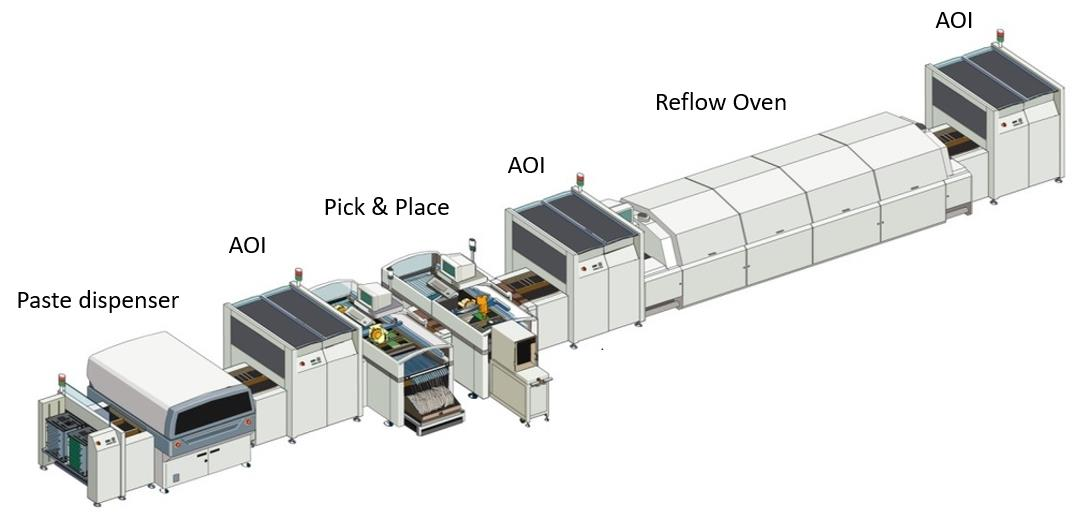
Pick and place machine
Sur la chaîne de montage, l’EMS place souvent plusieurs machines “pick and place” permettant de gérer le nombre de références différentes à équiper ainsi que leur nature.
Par exemple, une machine “pick and place” destinée aux résistances/condensateurs doit avoir une cadence élevée tandis qu’une machine destinée à de la connectique doit être capable de soulever des composants « lourds » avec une cadence sera moins élevée, qui s’explique par le nombre limité de ce type de composants.
Ce qui compte pour l’EMS (et qui impacte directement le coût de fabrication), c’est la gestion des goulots d’étranglement. Par exemple, la production est fluide si les temps de cycle sont uniformes sur chaque station. Mais c’est rarement la cas. Certaines stations ont des temps de cycles variables. Ce problème peut être géré en utilisant des étapes de stockage intermédiaires, en augmentant le nombre de postes, en modernisant les machines, etc.
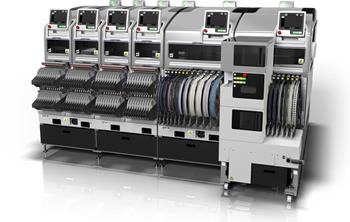
Four à refusion
Le four à refusion consiste en un four équipé d’un convoyeur permettant de suivre un profil thermique défini. Habituellement, les lignes SMT ne sont pas dédiées à un seul projet. Les profils thermiques du four dépendent du circuit imprimé, des composants, de la pâte à braser… Il est important que lors de la mise en place de la ligne, le service qualité vérifie que tous les paramètres soient correctement entrés dans la machine avant que la ligne ne commence à fonctionner. Ces contrôles doivent donner lieu à une checklist « Go For Prod ».
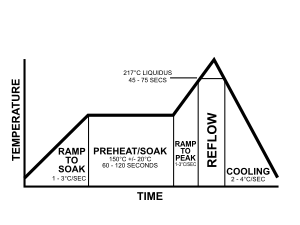
Profil thermique du four à refusion
Automated Inspection Control (AOI)
La plupart du temps, ces machines AOI sont utilisées à différentes étapes de la ligne SMT. Les AOI peuvent être placées après chaque étape (distribution de la pâte, pick and place, refusion…) mais comme tout cela à un coût (temps et matériel) des compromis doivent être fait en ce qui concerne goulot d’étranglement, temps de production, capacité de la machine, objectif de mise au rebut, etc. De nos jours, les AOI sont si efficaces qu’ils permettent de détecter les désalignements au micromètre, de vérifier les paramètres 3D des soudures, l’orientation des composants, etc. Au début de la production, ces machines doivent être paramétrées et même « entraînées » à filtrer les faux positifs.
L’emplacement des composants doit tenir compte de ces inspections optiques. Les grands éléments ne doivent pas être placés à côté de très petits. Dans le cas contraire, la couverture optique serait réduite et la carte électronique ne bénéficierait pas des avantages de ce puissant outil.
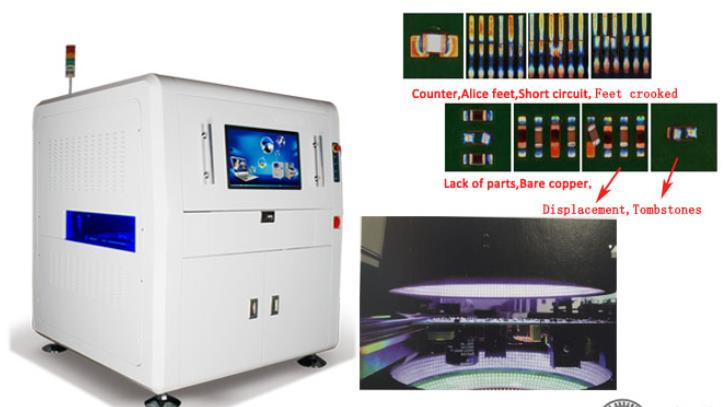
Machine AOI et quelques problèmes détectés
In-circuit tester (ICT)
Imaginez un multimètre multiplexé ultra-rapide capable de mesurer des composants passifs et actifs. Ajoutez-lui la possibilité de faire des tests de puissance et des capacités de programmation et vous obtenez l’ICT.
L’ICT permet de vérifier certaines caractéristiques d’un composant, son orientation, sa présence, s’il est en circuit ouvert ou en court-circuit ; ou bien de faire des tests diodes des entrées/sorties des circuits intégrés. Il est également possible de vérifier les rails d’alimentation, la consommation de la carte, d’effectuer des boundary scans ou même de programmer un circuit intégré.
Le principe de l’ICT repose sur le contact physique d’un lit à clou avec les signaux de la carte au moyen de points de tests. Il est donc très important d’ajouter autant de points de test que la conception le permet, en particulier lorsque l’ICT est nécessaire : c’est un outil puissant pour vérifier que les valeurs des composants sont dans la plage tolérée. Notez que l’ICT fourni une couverture de test basée sur la testabilité des composants. Le taux de couverture de test est calculé en fonction du type d’éléments testés et de la possibilité de faire ces mesures.
Prenons l’exemple d’une carte équipée d’un condensateur de 100 nanoFarads. Si vous avez des points de test des deux côtés du condensateur, vous pouvez tester sa présence, sa valeur, s’il est en circuit ouvert ou en court-circuit.
Prenons le même exemple, mais ajoutons un condensateur de 10microFarad en parallèle. Il ne sera possible d’effectuer le test de présence et de valeur que sur le condensateur 10microFarad car celui de 100 nanoFarad tomberait dans la tolérance de celui de plus forte valeur.
Les ICT sont souvent utilisés sur des assemblages de circuits imprimés panélisés pour réduire le temps de test cumulé.
En fonction de la complexité de la carte, le temps de cycle de l’ICT peut être assez long (plusieurs dizaines de secondes) et devenir le goulot d’étranglement de la ligne. De plus, la machine ICT étant coûteuse et non-pertinente pour toutes les conceptions, il est important d’arbitrer en spécifiant le besoin, le nombre de tests requis en fonction la complexité, l’application et le coût final de l’assemblage des circuits imprimés.
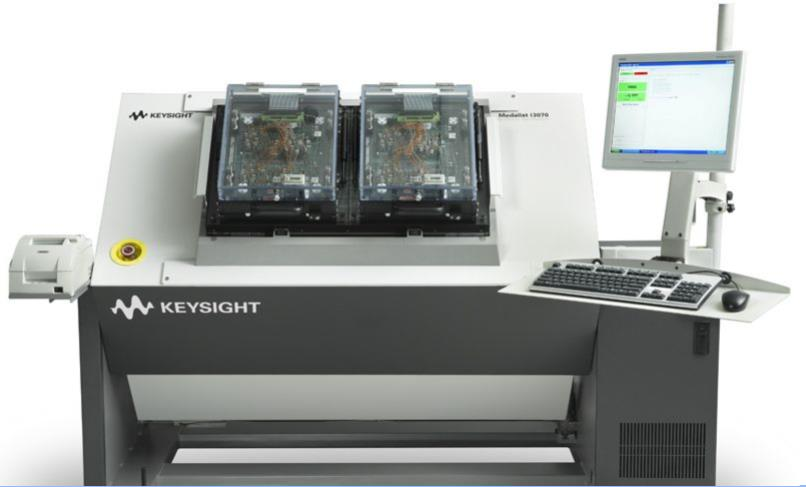
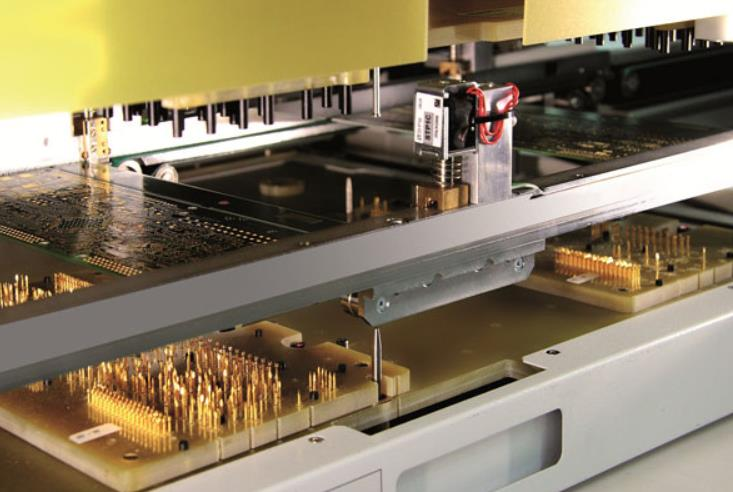
Depanel
Depanel est le procédé mécanique consistant à séparer chaque circuit imprimé de son panneau. De nombreux procédés existent, la plupart sont mécaniques et certains d’entre-eux peuvent endommager les composants présents sur les circuits imprimés. En effet, le depanel peut créer des contraintes mécaniques sur les circuits imprimés (exemple : des flexions) qui peuvent endommager les composants environnants. C’est aussi la raison pour laquelle il est recommandé de laisser de l’espace entre les bords des circuits imprimés voir d’effectuer des mesures de contraintes quand la criticité l’exige (pratique courante dans l’automobile).
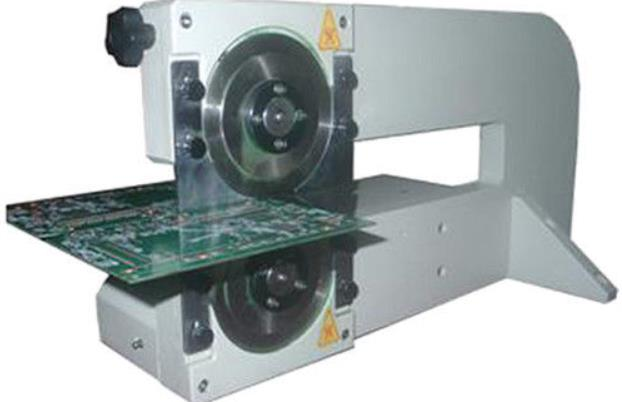
V-cut PCB depanelizer
Assemblage et tests fonctionnels
Si les étapes précédentes sont généralement exécutées dans le même ordre, l’assemblage et les test fonctionnels dépendent fortement de la conception du produit final et de la qualité attendue. Il est possible de vérifier chaque étape d’assemblage à l’aide de test de validation fonctionnels (FVT), de caméras ou d’un opérateur ; ou ne réaliser qu’un essai final une fois le produit assemblé. L’équilibre entre le temps de test (et donc le coût) et l’objectif qualité doit se faire selon le produit et son application.
Exemple : le « coût de la qualité » d’une automobile par rapport à un bien de consommation générique sera drastiquement différent car un défaut d’assemblage n’aura pas la même criticité pour le client final.
Processus d’assemblage
Une fois dépanélisés, les circuits imprimés peuvent être assemblés dans leurs boîtiers mécaniques finaux. Cette action est souvent réalisée à l’aide de gabarits d’assemblage qui permettent de s’assurer que les méthodes d’assemblage soient appropriées et répondent aux demandes des concepteurs. Une bonne pratique consiste à « détromper » la conception pour s’assurer qu’en aucun cas les composants ne peuvent être assemblés dans le mauvais sens. Il est par exemple possible d’ajouter une broche de centrage asymétrique sur le circuit imprimé correspondant au boîtier mécanique. Ces précautions ne doivent pas empêcher le concepteur de préciser quelles peuvent être les erreurs possibles ou même les critères de rebut.
Les assemblages sont la plupart du temps effectués par des opérateurs non qualifiés qui n’ont pas la connaissance du produit final et des contraintes de conception. Il faut donc se mettre dans la même position et demander, lors de la mise en place de la ligne, à des personnes non formées d’assembler le produit en analysant leurs gestes et leurs réactions à la lecture du document d’assemblage. Il sera alors possible d’observer des comportements difficilement prévisibles, de comprendre certaines difficultés et d’en tirer de meilleures pratiques, une mise à jour des guides d’assemblage voir même une mise à jour de la conception.
Essayer de faire des erreurs (sans faire d’action contre nature) sur chacune des étapes d’assemblage est également un bon moyen de vérifier si les bons outils sont utilisés, si le gabarit est suffisamment résistant pour supporter de mauvaises manipulations et si le process est suffisamment robuste pour détecter un mauvais assemblage par la suite.
FVT (functionnal validation tests)
Comme nous l’avons mentionné précédemment, les tests de validation fonctionnels (FVT) sont utilisés pour tester le produit pendant les différentes étapes de l’assemblage. Les FVT ont pour but de tester les différentes fonctions du produit et de valider leur fonctionnement pendant les exemples de tests fonctionnels : la simulation de la pression de boutons, le test d’afficheur mais aussi des tests électroniques tels que la vérification des tensions d’alimentation, le contrôles de bus de communication, etc…
Vouloir qualifier le produit au lieu de le valider sur le plan fonctionnel est une erreur couramment commise. La qualification (marge de conception, contrôles de comportement en limite de spécification…) est effectuée au stade de la conception et non pendant la production. Faire la qualification au moment de la production se solderait par un taux de rebut élevé en raison des limites étroites fixées pour un grand nombre de critères. Cette sur-qualité entraînerait des surcoûts importants.
La sur-qualité est aussi dangereuse que la sous-qualité. Elle peut drastiquement augmenter le prix final du produit ainsi que la charge des équipes qualité qui finira par avoir besoin d’un soutien technique de manière disproportionnée.L’évaluation de la ligne d’assemblage et des FVT peut être effectuée à l’aide de process qualité tel que GR&R (Gauge Répétabilité & Reproductibilité). Un exemple de ce test standardisé est d’assembler 30 produits différents sur chaque station avec 3 opérateurs non formés, de mesurer les ratios succès/échec et d’utiliser quelques formules statistiques pour déterminer l’efficacité du process mis en place.
Ce processus doit être complété par l’utilisation de « black sample » (ou « silver sample ») et de « golden sample ». Ces échantillons sont préparés par la R&D pour chaque station. Le « golden sample » est un échantillon R&D considéré comme une référence fonctionnelle auquel d’autres produits peuvent être comparés.
Les « black sample », également préparés par la R&D, ont des défauts connus qui doivent être détectés par les bancs de test FVT ou des postes de contrôle qualité.
Une fois de plus, un équilibre doit être trouvé quant à la criticité de la fonction par rapport au temps investi pour la tester. Attention à bien prendre en compte le développement nécessaire à ce type de détection qui peut parfois excéder plusieurs dizaines de milliers d’euros en R&D et le même montant en équipement.
En outre, le FVT fournit un score de couverture qui, ajouté à l’ICT et à l’AOI, donne le taux de couverture total.
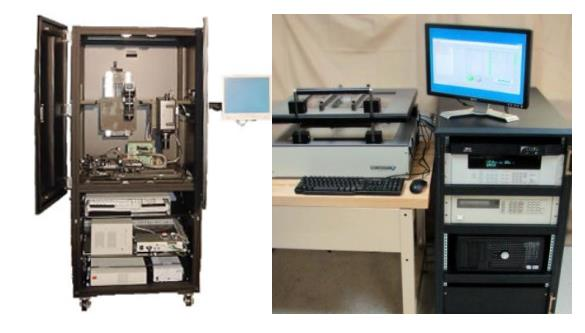
Functional Validation Testers (Left: TFT display tester, Right: PCBA functional tester)
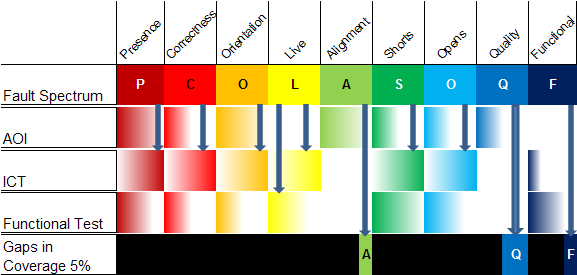
Typical test coverage score
OQC et expédition
Une fois le produit assemblé, des contrôles de qualité mis en place pour s’assurer que la production ne dérive pas de ses objectifs initiaux. Ces contrôles peuvent comprendre des tests « out of the box » (tests utilisateur), des vérifications esthétiques, etc.
Pour des raisons évidentes de temps de cycle, tous les produits ne peuvent atteindre ce niveau d’inspection. Un échantillonnage peut alors être mis en place pour s’assurer d’une qualité constante tout au long de la production. Des contrôles qualité spécifiques peuvent être ajoutés en fonction des problèmes remontés au cours du cycle de vie du produit. Par exemple, un échantillonnage étendu au début du cycle de vie de production ensuite rationalisé, un contrôle systématique d’une seule caractéristique si elle a provoqué des réclamations régulières de clients, etc.
L’étape finale du processus est l’expédition. Comme pour le matériel entrant, le packaging est très important.
Par exemple, il est possible d’utiliser le packaging final si le produit est prêt à être envoyé au client. Mais si le produit assemblé doit être packagé avec des accessoires (câbles, chargeurs…) dans un lieu différent ou reconditionné en raison de contraintes régionales, dans ce cas le choix d’un packaging intermédiaire est plus judicieux.Le packaging est important pour s’assurer que le produit ne sera pas endommagé pendant le transport (route, par bateau et/ou par avion cargo) et doit tenir compte des différentes contraintes de ces modes de transport.
Enfin, la palettisation doit être prise en compte pour optimiser les coûts d’expédition et facilite ainsi l’expédition dans le monde.
Traçabilité
Nous avons abordé certains processus et actions de contrôle qualité dans la section précédente. Mais les ingénieurs qualité n’ont pas seulement la responsabilité de s’assurer du respect des bonnes pratiques de production et d’assemblage ou de vérifier que la qualité reste stable dans le temps. Ils sont également en charge de la traçabilité des produits manufacturés en dehors de la ligne.Ces systèmes de traçabilité sont alimentés par des codes barres, des résultats d’essais ou d’autres commentaires. Les systèmes de traçabilité les plus avancés nécessitent que chaque étape individuelle soit démarrée et complétée par une action de traçabilité unique.
Prenons par exemple l’assemblage d’un PCBA dans un boîtier :
– Étape 1 : l’opérateur scanne le QR code du PCB
– Étape 2 : le système de traçabilité vérifie que le circuit imprimé est « autorisé » à participer à cette étape d’assemblage. En effet, un opérateur aurait pu « sauter » une station. Dans ce cas, l’ERP doit rejeter la pièce et un indicateur de qualité est déclenché.
– Étape 3 : le circuit imprimé est « autorisé », l’opérateur peut assembler le boîtier et le PCBA.
– Étape 4 : l’opérateur termine l’assemblage, il/elle prend un autre QR code et le colle sur le boîtier.
– Étape 5 : l’opérateur scanne ce QR code. Le sous-ensemble est maintenant dans le système et prêt pour la prochaine station.
Ce système de traçabilité permet également la gestion des stocks ainsi que la possibilité de remonter à la source d’un problème détecté plus tard dans le processus d’assemblage ou par le client final, et de prendre les actions correctives nécessaires.
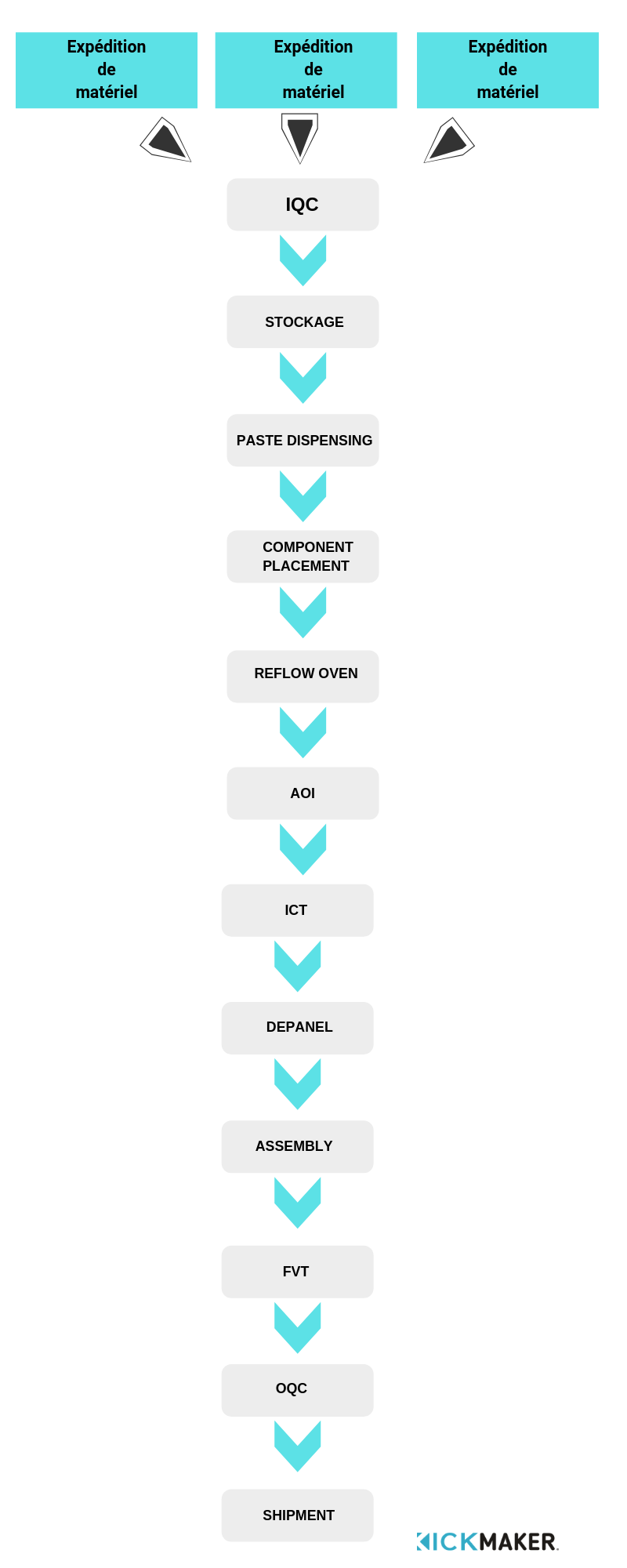
Glossaire
ERP : « Enterprise Resource Planning, signifiant littéralement en anglais, « planification des ressources de l’entreprise », et traduit en français par « progiciel de gestion intégré » (PGI) ».
EMS : » Le terme anglais Electronic manufacturing services (EMS) est couramment utilisée dans l’industrie électronique pour désigner les entreprises qui fournissent des services de fabrication en sous-traitance pour des produits électroniques : circuits imprimés (PCB en anglais), PCBA (assemblage de circuits imprimés, sous-ensembles). Les donneurs d’ordre sont alors souvent désignés comme OEM. Un EMS propose souvent en complément des activités de conception, validation, distribution et/ou service après-vente. Lorsque l’ensemble du développement est sous-traité, on parle d’ODM.
OQC : Dans la fabrication des circuits imprimés, le contrôle de la qualité, ou CQ en abrégé, est un processus par lequel les entités examinent la qualité de tous les facteurs impliqués dans la production. ISO 9000 définit le contrôle de la qualité comme « une partie du management de la qualité axée sur le respect des exigences de qualité ». Les produits finis doivent être inspectés avant la livraison, appelé OQC, hors contrôle qualité.
Rejoignez la communauté hardware
Inscrivez-vous à notre newsletter
Commentaires récents