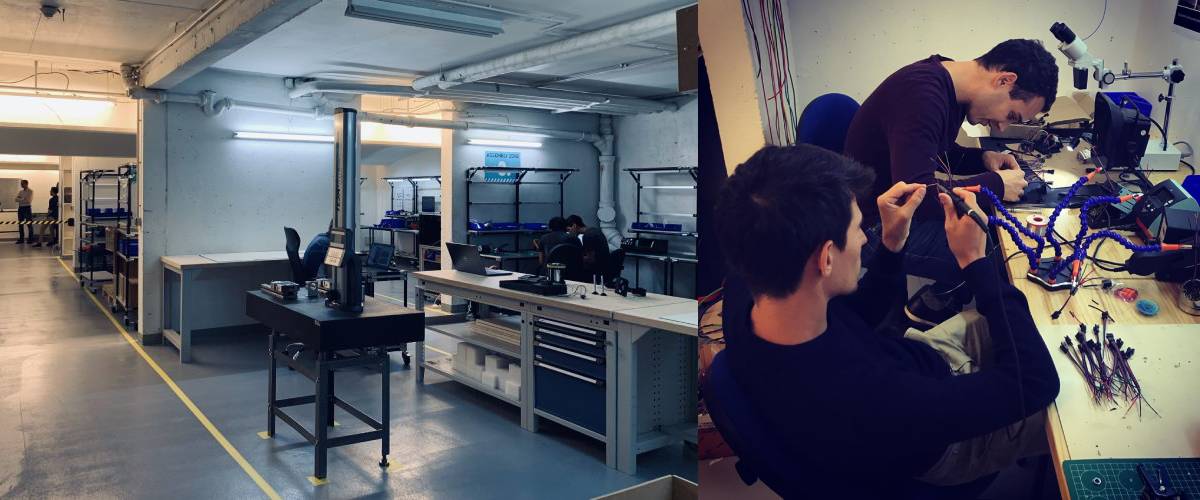
Il est souvent compliqué lorsque l’on se lance dans un projet hardware ou dans l’idéation d’un projet hardware, que l’on est investisseur ou conseiller de startups, ou simplement curieux, de trouver des informations claires sur l’industrialisation d’un produit high-tech. C’est ce que nous tenterons de faire de façon introductive, concise et non détaillée dans cet article.

Comme expliqué dans l’article précédent, l’industrialisation est un processus qui doit être robuste, fiable, reproductible et répétable et doit permettre à un prototype fonctionnel de devenir un produit manufacturable. Le verbe « industrialiser » signifie produire ou exploiter, selon des méthodes industrielles. (Découvrez quelle est la différence entre un prototype et un prototype industriel).
Il existe comme toujours plusieurs méthodes, mais celle dont nous vous parlerons aujourd’hui et que nous vous recommandons est composé de plusieurs étapes itératives et successivement menées, nommées EVT DVT PVT et désignant les différents niveaux de maturité du système à fabriquer et les différentes étapes du processus de fabrication. L’industrialisation commence après les POC pour Proof Of Concept (faisabilité des fonctions) et se poursuit parfois même après la livraison via des processus d’amélioration continue.
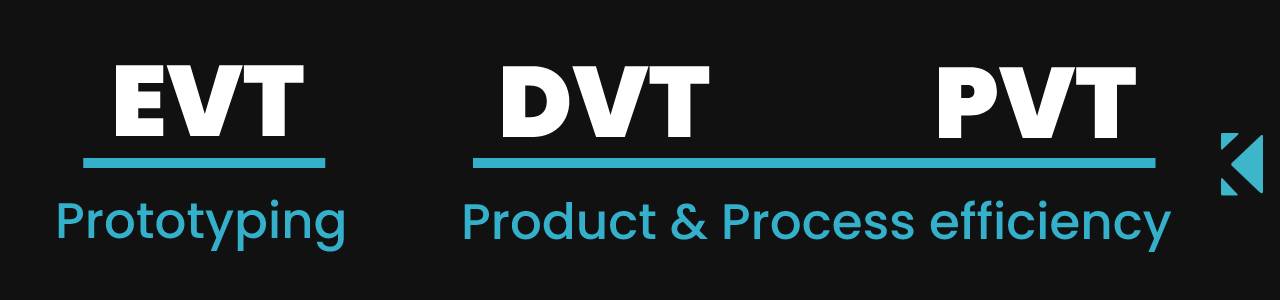
EVT
EVT signifie Engineering Verification / Validation & testing
-> C’est l’étape de validation des solutions techniques.
L’EVT combine les prototypes « looks like » et « works like » en un seul démonstrateur, et avec des pièces temporaires : pièces en dupli silicone, ou pièces de soft tooling imprimées en 3D, prototype PCBA…
L’EVT permet de vérifier que le prototype fonctionne avec toutes les fonctionnalités définies dans le cahier des charges ou PRD et que la conception répond bien à l’objectif de l’objet. Il faut s’assurer que l’on n’a pas fait fausse route sur la fonction.
Quantités de prototypes EVT : elles dépendent de la complexité du produit et du coût de la nomenclature (BOM) (3 à 10)
DVT
DVT signifie Design Verification / validation & testing
-> C’est l’étape de validation du produit
La phase DVT est entamée lorsque l’on est certain que le design fonctionnera. Les 3D et plans 2D sont terminés, les matériaux ainsi qu’un plan de test sont définis. Le produit DVT est censé être une configuration de conception de production finale, avec des composants issu de processus de production (des outils / moules finaux). Le design est testé avec de vraies pièces, vraiment aux cotes et avec des matériaux qui se rapprochent des matériaux finaux.
Pour cela, le produit est fabriqué en un nombre d’exemplaires limité et ces exemplaires subissent une batterie de tests (drop test, chaleur, usure…). Il est essentiel de s’assurer que le produit répondra aux exigences en matière de cosmétique (apparence) et d’environnement.
Cette étape est également très liée aux certifications et au contact avec les fournisseurs.
En résumé, on assemble, on test, on itère jusqu’à ce que le design convienne. À l’issue du DVT, un document de validation de tous les tests doit être fait et les 3D doivent être gelées.
Quantités : elles dépendent de la complexité du produit et du coût de la nomenclature (BOM) (50 à 100)
PVT
PVT signifie Product – Production Verification / Validation & Testing
-> C’est l’étape de validation de la ligne de production (préséries -> first run) :
L’étape PVT est la dernière construction du produit. Les unités fabriquées sont censées être vendues à des clients, si elles valident tous les tests. les pièces sont proches de celles qui seront utilisées pour la série, mais encore assemblées à la main. En général, le PVT est la transition directe vers la phase de montée en cadence et de mass-prod. Une chaîne de production pilote doit être établie pour vérifier qu’il n’y a pas de défaillance à un stade quelconque de la chaîne de production. La phase PVT valide le process d’assemblage : vitesse du process, qualité, points de contrôle et moyens de tests, outils de calibration et suivi de production, montée en compétences des ouvirers, packaging, flux d’approvisionnement et logistiques… Des process d’amélioration continue (PDCA, AMDEC manufacturing …) sont mis en place et permettront les évolutions et optimisations futures. Cette phase est davantage liée aux opérations qu’au développement.
Quantités : elles dépendent de la complexité du produit et du coût de la nomenclature (100 à 1000)
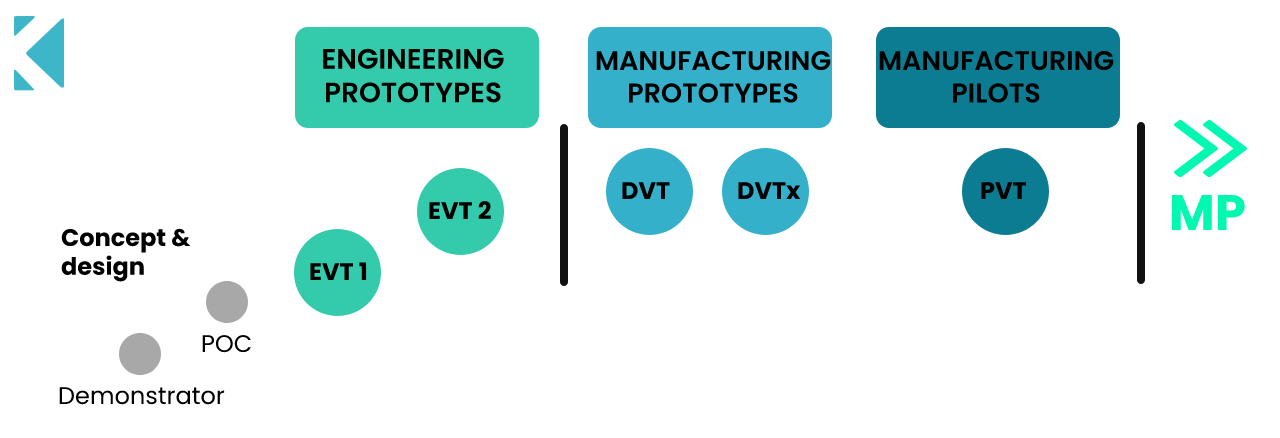
Commentaires récents