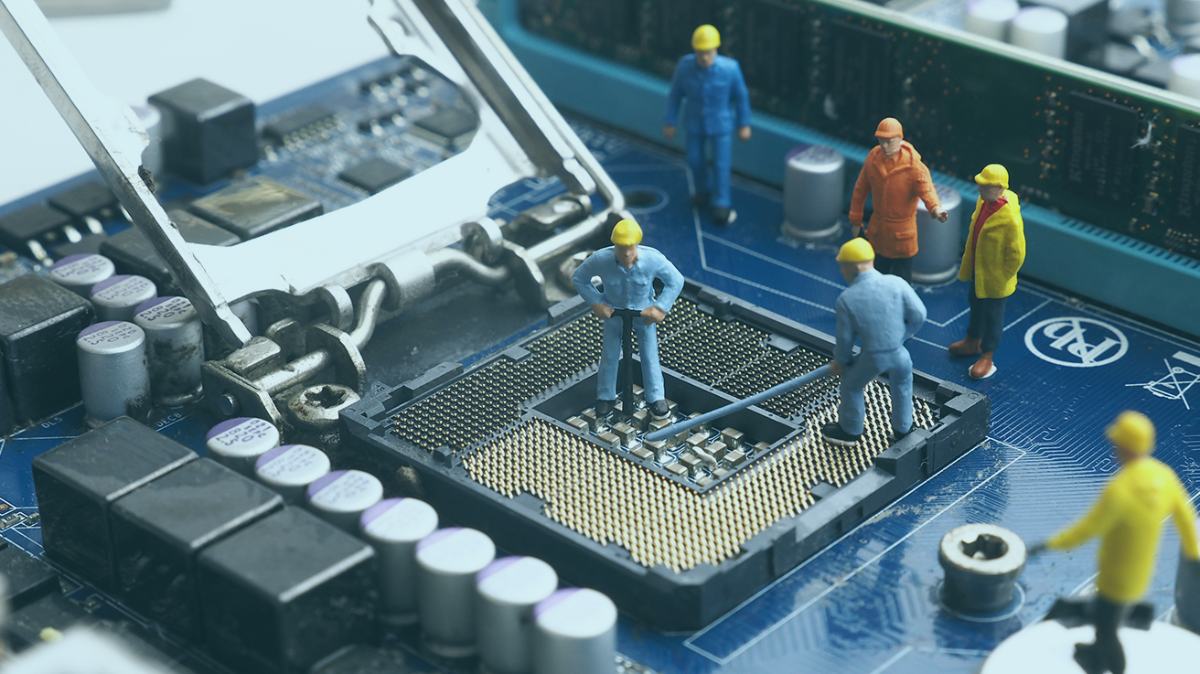
L’industrialisation aime les acronymes, et les acronymes le lui rendent bien. MP, FA, EPM, ODM, OPM, PRD, DRP, BOM, DFX, DFM [ETC] Parmi ces spécimens acronymiques, certains désignent des processus, d’autres des documents… Mais tous traitent de l’industrialisation. Si chaque secteur professionnel use de son propre jargon, celui de l’industrie plébiscite largement l’acronyme.
Ceux que nous allons traiter aujourd’hui se présentent sous la forme d’EVT/DVT/PVT.
Ces acronymes EVT DVT PVT désignent respectivement : Engineering Validation Test / Design Validation Test / Production Validation Test. Aujourd’hui, nous allons vous livrer notre vision de l’EVT/DVT/PVT, construite au fil de nos années d’expertise et de d’industrialisation produit.
Ces trois acronymes font référence aux différents stades d’industrialisation, entre le POC et la production série : du moins mature au plus mature. Ces différents stades existent pour minimiser les risques d’erreurs durant la production série. Les défauts dans la conception et le processus sont découverts durant ces étapes ; il est très important de les détecter tôt et de les détecter avant de se lancer dans la production série.
Ils permettent aussi de structurer le processus décisionnel. On part d’un nombre d’options larges que l’on réduit pour fixer ce nombre d’options et n‘avoir ensuite qu’à corriger/ajuster/optimiser.
En EVT on valide un scope fonctionnel, en DVT on stabilise et en PVT on adapte la production. À partir de la phase de DVT on ne touche plus au scope mais on corrige les erreurs, on ajuste les éléments et on optimise les performances.
On progresse par étape. Chaque étape apporte un degré supplémentaire de maturité et chaque itération produit de nouveaux prototypes. Si le résultat d’une étape n’est pas satisfaisant, on itère tout en gardant à l’esprit l’arbitrage délai/coût/qualité. Chaque itération à un coût et implique des délais supplémentaires.
Chacune de ces phases est cyclique et intègre des sous-phase de 1) design 2) prototype 3) validation. En général ces sous-phases ne dépassent pas le nombre de trois. Ainsi vous aurez EVT 1 EVT 2 EVT3. Le principe est le même pour le DVT à la différence près que les sous-phases s’effectueront sur un scope de produit final et en utilisant des outils qui au fil du DVT deviendront finaux
Concernant le PVT, il s’agit :
1- installation de la ligne de production
2- revue de la ligne
3- test de production
4- FAI (first article inspection) + rapports
Puis identification des points de faiblesse => retour à 1 pour amélioration continue.
À la fin de PVT, on valide le golden sample plus tous les moyens de production pour passer en MP (mass-production) qui sera elle aussi soumise à un mouvement d’amélioration continue.
En amont de l’EVT/DVT/PVT se trouve la phase de prototypage qui amène à une preuve de concept. Il y a les prototypes “looks like” qui valident le design, l’aspect extérieur, l’usage ; et la preuve de concept “works like” qui prouvent les fonctions produit.
Si vous souhaitez en savoir plus sur ce qu’est un bon prototype industriel, n’hésitez pas consulter notre article qui traite du bon déroulement d’un projet industriel.
Article réalisé avec l’aide précieuse de Stépane Tampigny et Alexis Foiret, ingénieurs chez Kickmaker
EVT : Engineering Validation Test
Définition :
Une fois que le hardware est finalisé, il a besoin d’être testé et validé. Cette étape est appelée EVT.
Cette phase EVT sert à vérifier que le prototype fonctionne avec toutes les fonctionnalités définies dans le PRD, et que l’objectif de l’objet soit bien rempli (exemple : fabriquer un aspirateur qui aspire réellement). La phase EVT permet donc de s’assurer que le projet ne fait pas fausse route sur la fonction. Les DFX dont d’ores-et-déjà intégrés au processus.
Objectifs :
En pré EVT: tester tout ce qu’on veut mettre dans le produit (souvent en pré études indépendantes)
En EVT : identifier les problèmes qui doivent être résolus avant la conception, produire des prototypes offrant les fonctionnalités clés, avec des composants existants ou encore en stade de mise au point, dans la taille voulue. Intégrer ce qui était du POC avant pour arriver en fin d’EVT à un scope fixé réalisable
Quantité :
Entre 1 et 5 par cycle de prototypage. Pour valider l’EVT, une dizaines de prototypes seront nécessaires pour un produit moyen.
Moyens :
Prototypage rapide, impression 3D, découpe laser carte électronique conçue sur mesure ; mécanique conçue sur mesure etc.
Résultats :
Prototype dans la taille voulue, fonctionnalités clés présentes sur le produit. Les composants et les technologies sélectionnés peuvent atteindre le coût souhaité.
Livrable :
Prototype qui contient les fonctions souhaitées.
Limites :
En général, prototype à l’état cosmétique brut : pas d’état de surface, de finition de surface, de couleur… Mais tout dépend de l’importance de la cosmétique dans votre produit. Si le design ou l’encombrement sont des fonctionnalités majeures, alors vos prototypes et mockup les plus en amont afficheront déjà le design final pour pouvoir concevoir l’électronique et la mécanique par rapport au design final.
En général : pas d’optimisations (coûts, technos…) et certaines fonctionnalités secondaires peuvent manquer.
DVT : Design Validation Test
Définition :
La phase de DVT est entamée lorsque l’EVT est validé et qu’il est certain que le design est fonctionnel. Le DVT sert à effectuer les validations que le client demande sur un design figé. Il est rare que la conception soit correcte du premier coup, donc on itère sur le design jusqu’à ce que le produit soit parfait.
Lors du DVT, on teste le design avec des vraies pièces aux cotes et avec des matériaux qui se rapprochent de ce que l’on veut obtenir . En parallèle de quoi il faut prendre contact avec les fournisseurs pour commencer à produire les différentes pièces finales.
En milieu/ fin de phase on teste même les pièces injectées. On utilisera les moules finaux qui seront ajustés au fur et à mesure (correction mineures, traitement de surface, ajustement des paramètres, débug et débruitage pour l’électronique …). En fin de phase on doit avoir un produit aux spécifications finales validées car idéalement la phase de PVT ne sert qu’à la validation des moyens de production (ligne d’assemblage , jigs et test bench…)
Durant cette phase de DVT, il est possible de faire des choix de pièces ou de matières volontairement temporaires qui permettront une production en peu d’exemplaires (ex : pièces injectées mais avec moule silicone qui ne va durer qu’une vingtaines d’injections mais va permettre de faire des tests de validation). Remarque, en dupli silicone on dépasse rarement 20 tirages de pièces. En effet, avec cette technologie, les PU utilisées sont des bi-composants Isocyanate et polyol. Une fois ces 2 composants mélangés, et une fois la coulée effectuée, la mise sous vide effectuée et le tps de pot life passé, le matériau devient exothermique. Il attaque donc le silicone en surface au fur et et mesure des tirages. Le fait de devoir ensuite démouler les pièces en tordant et déformant les moules (comme moules silicone de gâteaux), endommage également les propriétés du moule silicone. À cette étape, il vaut mieux utiliser tous les composants finaux. Sauf si on décide de commercialiser le produit en l’état, c’est à dire avec pièces PU, ou impression 3D pour des raisons économiques ou marketing. Ça se pratique.
Le produit doit être conçu en petites quantités et soumis à différents stress afin de tester la résistance, l’étanchéité, la sûreté… Une large batterie de tests sera nécessaire pour déterminer si le produit est prêt pour la production ou non. Tout comme l’EVT, les DFX sont travaillés durant cette étape.
Les produits DVT servent à toutes les validations laboratoire (Aging, Cycle thermique et climatique, vibratoire, packaging, chute, tenue chimique, biocomp…) C’est également à cette étape que sont intégrées les problématiques de certification. Lors de la phase DVT, les produits ne devraient utiliser que des pièces issues de moyenne série de production. Et non des pièces via Dupli Silicone.
Objectif :
Produire des prototypes ayant toutes les fonctionnalités, avec les composants prévus pour la production en série, pouvant servir aux certifications (CE) et identifier les problèmes potentiels qui doivent être résolus avant la conception.
Réaliser/industrialiser et rejeter ce qui finalement n’est pas faisable ou trop coûteux (qualité vs fonctions vs prix vs objectif de vente) pour arriver à un produit final en fin de phase.
Quantité :
Généralement entre 20 à 100. Tout dépend de la volumétrie en MP (mass-production) et du coût d’un prototype. La certification demande un certain nombre d’exemplaires et la validation consomme à elle seule au moins entre 20 et 30 prototypes. Sans compter ceux nécessaires pour le marketing.
Moyens :
Prototypage rapide, composant sur mesure ; mécanique sur mesure, matériel industriel.
Livrable :
Document de validation de tous les tests, 3D gelées et remises d’équerre.
Résultat :
Prototypes fonctionnels, prêts à produire en série, sans défauts majeurs. Certains prototypes peuvent être distribués à des «beta testeurs» ou montrés à des futurs clients. Les DVT peuvent servir aux tests de certification.
Limites :
Les pièces mécaniques ne sont pas finales et leur aspect cosmétique peut être imparfait.
PVT : Production Validation Test
Définition :
Le PVT est la dernière phase d’industrialisation, l’étape finale avant la production en série qui permet d’envoyer les premiers produits aux clients, souvent les backers des plateformes de crowdfunding. Lors de cette phase PVT, le design est figé et on valide le process d’assemblage. Les pièces sont proches de la série mais assemblées à la main. On simule l’assemblage à la chaîne pour éprouver le process d’assemblage.
C’est donc à cette étape que l’assembleur exécute la ou les lignes de production planifiées en utilisant tous les équipements finaux, les processus et les étapes d’assurance qualité.
Lors de la phase de PVT, les DFX sont corrigés, les bancs de tests et moules de production série sont conçus et idéalement on fait des petits ajustements mécaniques. Il est très courant à ce stade de trouver des problèmes d’assemblage, et cela peut inclure des changements de conception des plastiques et des PCBA pour minimiser les déchets de rendement, optimiser l’assemblage si l’impact coût est important ou optimiser certaines pièces si l’AMDEC fait ressortir des faiblesses…. Tous les composants et processus doivent se trouver à l’étape de production en série prévue, ce qui comprend l’emballage, la logistique, l’expédition du fret et les contrôles d’assurance qualité.
La ligne de production doit être optimisée pour le produit, en réduisant si possible le temps entre chaque étape, et en rendant le process entier aussi fluide et fiable que possible.
Quantité :
Entre 50 et 200.
Objectifs :
Vérifier les rendements de production de masse à des vitesses de production de masse. Prouver que le process de production et de tests en usine est opérationnel -> on prend un produit fini et on construit une chaine de production optimisée pour la série.
Moyens :
Électronique et composants finaux. Pièces mécaniques provenant des moules de production.
Résultat :
Validation que les produits en fin de chaîne sont conformes à la conception.
Livrable : produit final en quantité limitée.
Limites :
Le temps nécessaire pour la production peut encore être élevé. Toutes les procédures ne sont pas encore écrites.
Toutes ces grandes étapes ont été simplifiées pour que cet article soit digeste. Quoi qu’il arrive, fabriquer un produit est une grande aventure et un long voyage. Avoir un aperçu des différentes étapes, même rapide, peut vous aider à éviter les problèmes.
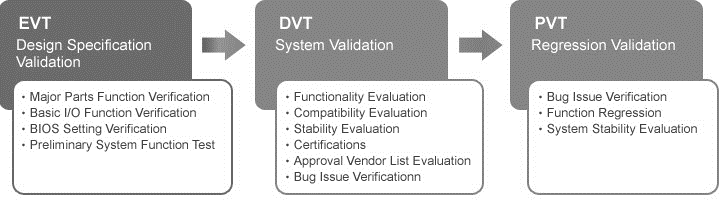
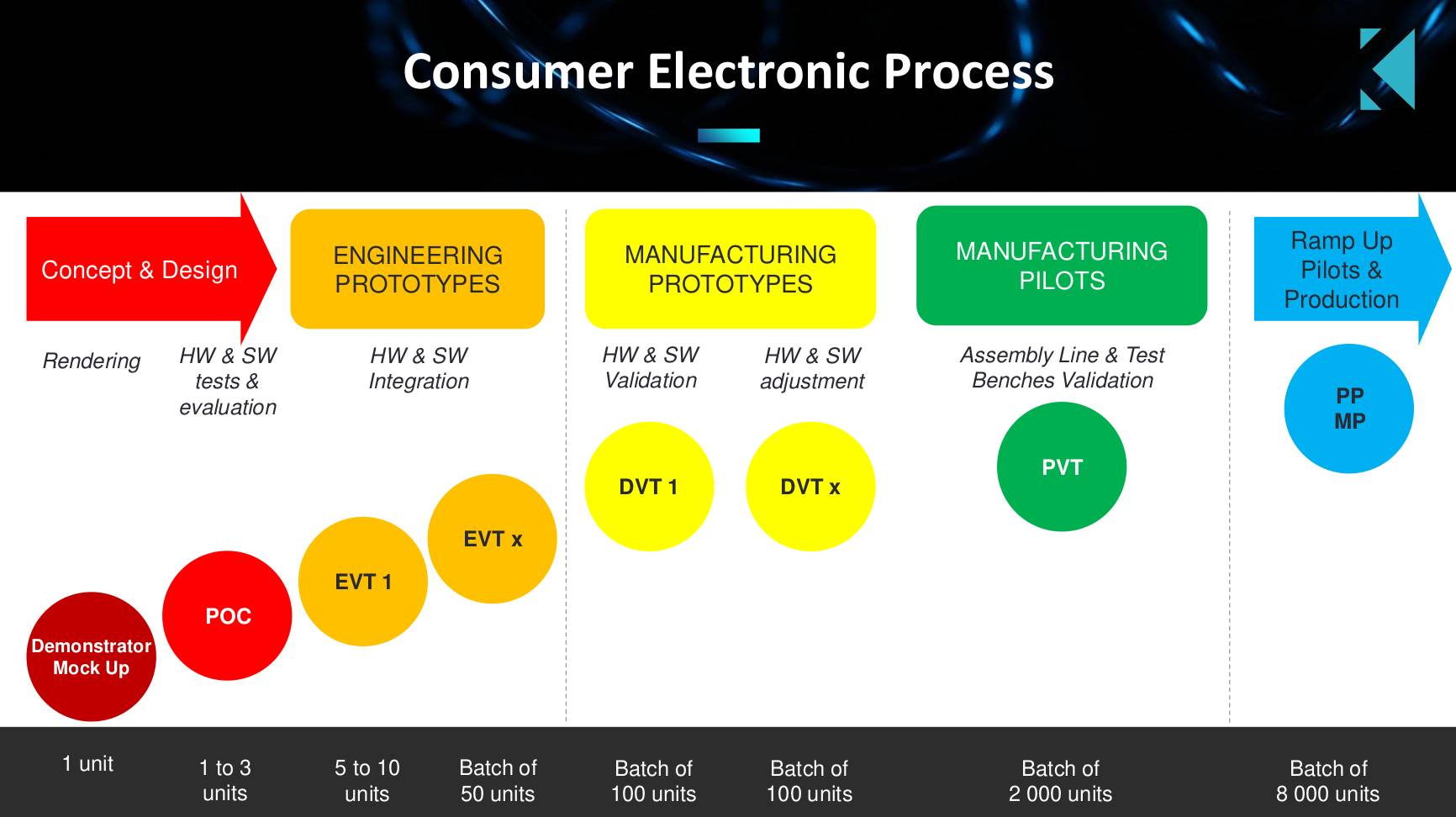
Glossaire
DFX : Design for X
Design l’ensemble des processus permettant d’optimiser la conception d’un produit
- “DFA Design for Assembly : conception de produits favorisant l’assemblage
- DFM Design For Manufacturing ou Design For Manufacturability : conception de produits favorisant la fabrication
- DFMA 1/ Design for Manufacturing (ou Manufacturability) and Assembly – en français : conception de produits favorisant la fabrication et l’assemblage 2/ Design for Maintenance : conception de produits favorisant la maintenance
- DFP Design For Producibility : conception de produits favorisant la production (producibility : facilité de production)
- DFP Design For Procurement : consiste à choisir des composants ou des schémas de supply chain visant à faciliter la vie série (fiabilité des fournisseurs, optimisation des lead time)
- DFR Design for Reliability : conception de produits favorisant la fiabilité
- DFS Design for Services conception de produits : favorisant les services”
POC : Démonstration de faisabilité. Prototype destiné à démontrer la faisabilité d’un projet. Il intervient très en amont de la phase développement produit, avant le prototype fonctionnel.
PRD : “Un PRD a pour but de fournir le niveau de détail nécessaire à l’équipe de développement pour lui permettre de comprendre les capacités, les fonctionnalités et les caractéristiques du produit, nécessaires pour répondre aux besoins du marché identifié dans le MRD.”
Retrouvez les informations dans notre article : déroulement d’un projet industriel.
Commentaires récents