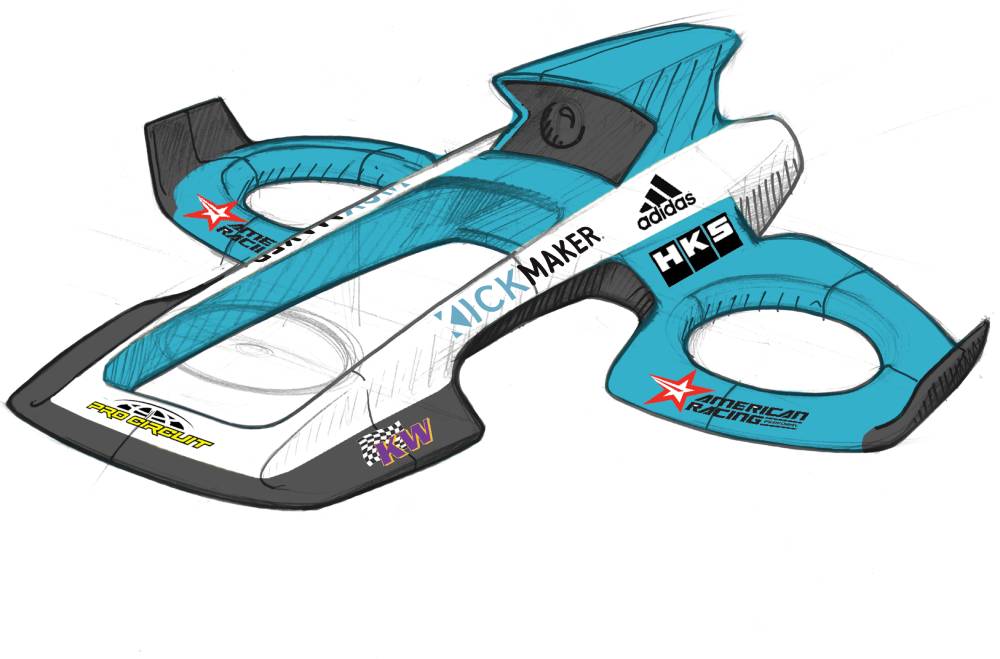
At Kickmaker, our design process involves technical conception aimed at establishing a cohesive product structure that effectively addresses various industrial challenges. This encompasses considerations such as technical feasibility, economic viability, ergonomic factors, and functional requirements.
While we don’t specialize in industrial design alone, we collaborate closely with design agencies like Elium Studio. Nonetheless, there are instances where we actively contribute to design initiatives.
A tripartite creative process
The process of product creation involves a collaborative effort among Kickmaker, the client, and the design agency. Typically, the client engages with a design agency initially, followed by consultation with industrial partners, with us at Kickmaker being the second point of contact.
The client communicates their vision to the designers, who outline the product’s external appearance and initial functionalities, providing us with preliminary drawings or 3D files representing the surface features. Subsequently, discussions ensue. We evaluate these proposals, considering technical feasibility, alignment with intended functionalities, and budgetary constraints, and then share our feedback.
Based on our input, the designers iterate on their proposals, from which the client selects one for further development. We then commence the process of transforming the chosen design into a model ready for industrial production. This involves detailing technical specifications, incorporating ergonomic considerations and usage scenarios in collaboration with the client, and engaging mechanical, electronic, and mechatronics teams.
Utilizing 3D modeling, we visualize design concepts, ensuring compatibility with technical requirements, assembly management, industrialization processes, cost efficiency, and potential manufacturing partners. As industrial experts, we harmonize aesthetic and practical aspects with the product’s manufacturability, providing crucial support to design agencies in refining their concepts.
Once an industrializable model is crafted and shared with the design agency, roles switch, and they provide us with feedback, initiating a phase of fine-tuning. This collaborative journey navigates negotiations among aesthetics, usability, ergonomics, functionality, and industrial feasibility, culminating in a compromise satisfying all stakeholders.
Friction point : a design too far removed from industrial constraints
At times, design agencies stray too far from the practicalities of industrial product design, conceptualizing products that pose significant challenges for actual manufacturing. In such instances, we step in to refine the design.
Conversely, some agencies delve deeply into considerations like structural integrity, assembly processes, and user interfaces, facilitating collaboration among all stakeholders – themselves, us, and the client. They understand, for instance, that realizing a particular volume may necessitate splitting it into multiple parts.
Design agencies with a focus on industrial design, backed by experience and a history of collaboration with engineering departments, possess a nuanced understanding of industrial constraints, such as geometric compatibility with materials. They conduct thorough preliminary work, addressing production issues upfront.
These constraints encompass various aspects:
- Spatial limitations: Electronics may offer modularity, but constraints often arise around mechanical components and batteries. Technological boundaries can restrict the object’s size.
- Manufacturing considerations: Products must be moldable and demoldable. Smooth, expansive surfaces favored by agencies can pose manufacturing complexities, necessitating thoughtful joint placement.
- Material constraints: Factors like durability, aesthetics, special properties (such as transparency), biocompatibility, and eco-design considerations play vital roles in material selection.
Navigating these constraints effectively requires a collaborative approach, ensuring that design aspirations align with industrial feasibility, resulting in products that seamlessly blend creativity with practicality.
Kickmaker’s microfactory
Thanks to a microfactory dedicated to the assembly of high-tech products, which we have named KAL for Kickmaker Assembly Line, we prototype, iterate and test a wide range of shapes and materials. We give ourselves the means to be quite reactive. Kickmaker engineers have a big maker component, a more open vision than a traditional engineer with multiple skills. We don’t just execute a specification file, but look for innovation and optimization. In many cases, we go beyond conventional engineering, because we work on many innovative projects that require research into processes, materials, technologies and industrial partners.
We have a pool of talent who know how to do things themselves, with a design approach. We can start testing a design with 3D printers, mechanical properties (clips, screw barrels, interlocking) or aesthetic rendering in terms of materials: moving from all-plastic to bio-sourced products, for example, or calling on our vast network of suppliers and prototypists. Thanks to the KAL, we can produce semi-finished products in small batches, or functional finished products with materials, as well as assembly ranges, assembly line set-ups and pre-certification tests.
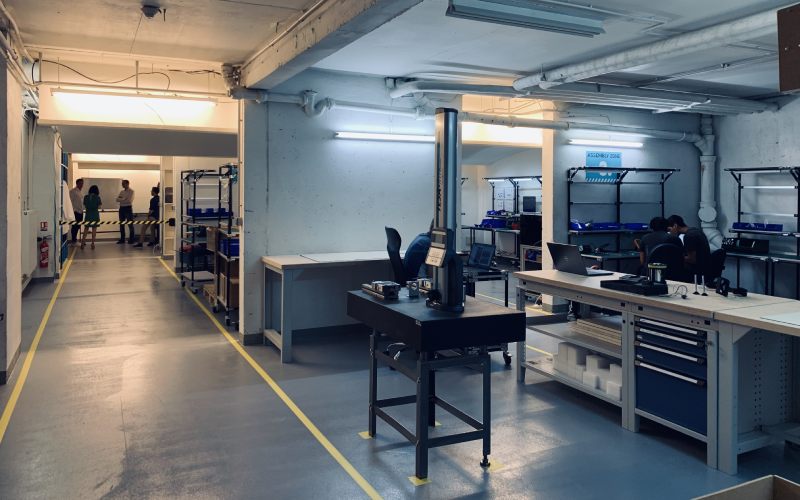
Recent Comments